Why do the slitter knives and tools for precision slitting of metal sheets need to be very precise?
Views : 3008
Author : Yuan Feng
Update time : 2021-05-26 14:37:15
Precision cutting of metal sheets requires precision knives and tools for two purposes:
1) The accuracy and constancy of the clearance must be maintained at any time and at any position during cutting. This is the core issue of precision cutting of sheet metal. Specifically, the clearance issue involves the following aspects:
a. Nominal clearance. It is determined by the material, hardness, and thickness. For some thin materials, they even require micron-level precision clearances. For example, a duralumin plate with a thickness of 0.07 mm requires a clearance of 0.0042 mm. If there are only spacer rings with 10 microns level (0.01 mm) accuracy, it cannot meet the above clearance requirements anyway. Although for precision cutting of most thin metal plates, the thickness dimension of the spacer ring must reach 10 microns level (0.01 mm) accuracy, but for ultra-precision thin plate cutting, the spacer ring must reach the micron level accuracy.
b. Dynamic clearance. The cutting of round knives is a 360° rotating rolling shear. During rolling, the clearance formed by the upper and lower round knives in the contact area changes continuously with the rotation of the two round knives. If the two round knives are made absolutely correctly, the clearance should be constant and there will be no change, but once the two round knives are made incorrectly, the plane near the outer circle of the two round knives will drift laterally when they rotate, resulting in a change in the clearance. For example, the runout of the sideface of two round knives is 5 μm, but the direction is opposite, the maximum clearance between the two knives can reach 0.01 mm, and the min. can reach 0 mm. For the 0.07 mm duralumin plate in the above example, the nominal clearance of 0.0042 mm is required, and the error is almost 100%, which is absolutely not allowed. In this case, if the accuracy of the tool is worse, the two knives will also have the phenomenon of biting. Therefore, in order to keep the dynamic clearance constant, a geometric tolerance must be set for the round knife. For precision cutting of metal strips, the flatness, including sideface runout, must be within 2 μm.
c. The cumulative error of the clearance. Except for a few slitting machines used for pre-cutting, most slitting machines can cut more than 2-3 strips. The slitting machine with the largest number of strips can reach 81 strips. For each strip, the tool needs a male knife unit and a female knife unit, and each cutting unit is generally composed of 3 to 5, or even 6 to 7 round knives, bonded stripper rings, and spacers. Here is a most common example to illustrate the importance of the cumulative error of the clearance. If we cut only 5 strips, and each unit consists of only 4 tools, then there are only about 20 tools on the upper and lower arbor. The purchased tools are very precise, tolerances are all "zero", and the thickness errors are all within ±1 μm. Considering the randomness of tool placement, we assume that the thickness of the tools on the upper arbor are all "+0.5 μm", and the thickness of the tools on the lower arbor are all "-0.5 μm". In this case, when cutting the last strip, the last knife on the upper shaft is offset from the standard position 10 μm on the operating side, and the last knife on the lower shaft does not reach the standard position 10 μm on the operating side. So the clearance reaches 0.02 mm. For thin materials, this clearance error is too large. But if the number of strips is 20 and the number of tools in the cutting unit is 6, the cumulative error caused by this will reach 0.12 mm. What’s worse, if the thickness of the tools on the upper shaft is "-0.5 μm", and the tools on the lower shaft are all "+0.5 μm", then the two knives will touch each other when the upper shaft goes down. This is the so-called "bite knife". If "biting knife" occurs, not only the product will not be cut properly, but the tool will also be damaged.
From the above analysis, it can be seen that even if the accuracy of the tool is so high, it will encounter the cumulative error, and we have to use other methods to eliminate its cumulative error. If the thickness error and tolerances of the tool are not good, or even poor, no one can combine them into precise cutting units to cut precision thin coils. Therefore, in order to eliminate the cumulative error of the clearance, all tools, including round knives, bonded stripper rings, spacers, and thickness tolerances must be precise enough. At present, some companies, such as China Goodklife, have been able to manufacture tools with thickness tolerances within ±1 μm and flatness and parallelism within 2 μm.
d. The first clearance. As the name implies, the first clearance is formed by the first knife of the upper and lower shafts close to the shoulder of the shaft. If the knife is made very precise, but the shoulders of the upper and lower knife shafts are misaligned with each other, then the original ideal clearance between the two sides of each strip will change, one side becomes larger and the other side becomes smaller. It will be displayed regularly. One side of each strip is not continuously cut, and the other side has serious burrs. There are often slitting machine manufacturers who are unable to solve this problem before the machine leaves the factory. This requires the user to be concerned about this problem, and rely on the thin spacer ring provided by the precision tool manufacturer to adjust the correct first clearance.
2) The width of the strip to be cut must meet the requirements of the nominal size and its tolerances. In order to ensure the quality of the downstream products of the metal strip, in addition to edge burrs and strip plane bending, users often place high requirements on the width of the strip to be cut. For the strip material used to make the pipe, if its width is not uniform, the weld seam of the pipe rolled out by it will change too much, and the quality of the weld will naturally be poor. For high-end wine bottle caps, if the width is not uniform, the material will either jam or break in the progressive die, which will affect production, or it will shake in the progressive die, which will affect the quality of the cap.
From these two purposes, our cutting tools must be very precise and sometimes ultra-precise. Table 1 shows the precision level of slitting tools from Goodklife. Figure 1 is the photo of precision pre-inspection of slitting knife.
1) The accuracy and constancy of the clearance must be maintained at any time and at any position during cutting. This is the core issue of precision cutting of sheet metal. Specifically, the clearance issue involves the following aspects:
a. Nominal clearance. It is determined by the material, hardness, and thickness. For some thin materials, they even require micron-level precision clearances. For example, a duralumin plate with a thickness of 0.07 mm requires a clearance of 0.0042 mm. If there are only spacer rings with 10 microns level (0.01 mm) accuracy, it cannot meet the above clearance requirements anyway. Although for precision cutting of most thin metal plates, the thickness dimension of the spacer ring must reach 10 microns level (0.01 mm) accuracy, but for ultra-precision thin plate cutting, the spacer ring must reach the micron level accuracy.
b. Dynamic clearance. The cutting of round knives is a 360° rotating rolling shear. During rolling, the clearance formed by the upper and lower round knives in the contact area changes continuously with the rotation of the two round knives. If the two round knives are made absolutely correctly, the clearance should be constant and there will be no change, but once the two round knives are made incorrectly, the plane near the outer circle of the two round knives will drift laterally when they rotate, resulting in a change in the clearance. For example, the runout of the sideface of two round knives is 5 μm, but the direction is opposite, the maximum clearance between the two knives can reach 0.01 mm, and the min. can reach 0 mm. For the 0.07 mm duralumin plate in the above example, the nominal clearance of 0.0042 mm is required, and the error is almost 100%, which is absolutely not allowed. In this case, if the accuracy of the tool is worse, the two knives will also have the phenomenon of biting. Therefore, in order to keep the dynamic clearance constant, a geometric tolerance must be set for the round knife. For precision cutting of metal strips, the flatness, including sideface runout, must be within 2 μm.
c. The cumulative error of the clearance. Except for a few slitting machines used for pre-cutting, most slitting machines can cut more than 2-3 strips. The slitting machine with the largest number of strips can reach 81 strips. For each strip, the tool needs a male knife unit and a female knife unit, and each cutting unit is generally composed of 3 to 5, or even 6 to 7 round knives, bonded stripper rings, and spacers. Here is a most common example to illustrate the importance of the cumulative error of the clearance. If we cut only 5 strips, and each unit consists of only 4 tools, then there are only about 20 tools on the upper and lower arbor. The purchased tools are very precise, tolerances are all "zero", and the thickness errors are all within ±1 μm. Considering the randomness of tool placement, we assume that the thickness of the tools on the upper arbor are all "+0.5 μm", and the thickness of the tools on the lower arbor are all "-0.5 μm". In this case, when cutting the last strip, the last knife on the upper shaft is offset from the standard position 10 μm on the operating side, and the last knife on the lower shaft does not reach the standard position 10 μm on the operating side. So the clearance reaches 0.02 mm. For thin materials, this clearance error is too large. But if the number of strips is 20 and the number of tools in the cutting unit is 6, the cumulative error caused by this will reach 0.12 mm. What’s worse, if the thickness of the tools on the upper shaft is "-0.5 μm", and the tools on the lower shaft are all "+0.5 μm", then the two knives will touch each other when the upper shaft goes down. This is the so-called "bite knife". If "biting knife" occurs, not only the product will not be cut properly, but the tool will also be damaged.
From the above analysis, it can be seen that even if the accuracy of the tool is so high, it will encounter the cumulative error, and we have to use other methods to eliminate its cumulative error. If the thickness error and tolerances of the tool are not good, or even poor, no one can combine them into precise cutting units to cut precision thin coils. Therefore, in order to eliminate the cumulative error of the clearance, all tools, including round knives, bonded stripper rings, spacers, and thickness tolerances must be precise enough. At present, some companies, such as China Goodklife, have been able to manufacture tools with thickness tolerances within ±1 μm and flatness and parallelism within 2 μm.
d. The first clearance. As the name implies, the first clearance is formed by the first knife of the upper and lower shafts close to the shoulder of the shaft. If the knife is made very precise, but the shoulders of the upper and lower knife shafts are misaligned with each other, then the original ideal clearance between the two sides of each strip will change, one side becomes larger and the other side becomes smaller. It will be displayed regularly. One side of each strip is not continuously cut, and the other side has serious burrs. There are often slitting machine manufacturers who are unable to solve this problem before the machine leaves the factory. This requires the user to be concerned about this problem, and rely on the thin spacer ring provided by the precision tool manufacturer to adjust the correct first clearance.
2) The width of the strip to be cut must meet the requirements of the nominal size and its tolerances. In order to ensure the quality of the downstream products of the metal strip, in addition to edge burrs and strip plane bending, users often place high requirements on the width of the strip to be cut. For the strip material used to make the pipe, if its width is not uniform, the weld seam of the pipe rolled out by it will change too much, and the quality of the weld will naturally be poor. For high-end wine bottle caps, if the width is not uniform, the material will either jam or break in the progressive die, which will affect production, or it will shake in the progressive die, which will affect the quality of the cap.
From these two purposes, our cutting tools must be very precise and sometimes ultra-precise. Table 1 shows the precision level of slitting tools from Goodklife. Figure 1 is the photo of precision pre-inspection of slitting knife.
Table 1 Goodklife Circular Knife Tolerance
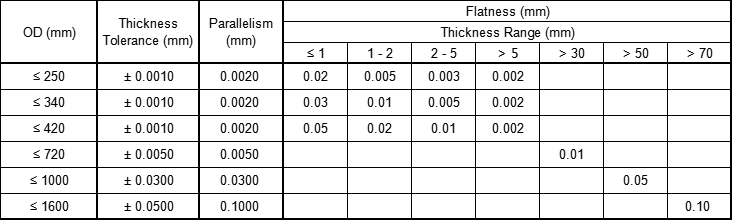
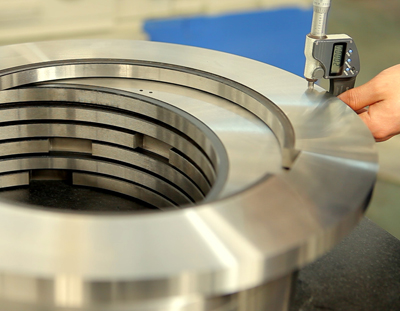
Figure 1 Precision Pre-inspection of Slitting Knife
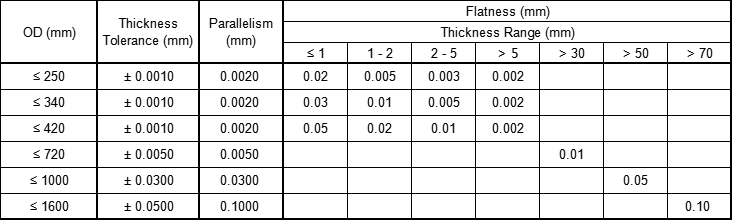
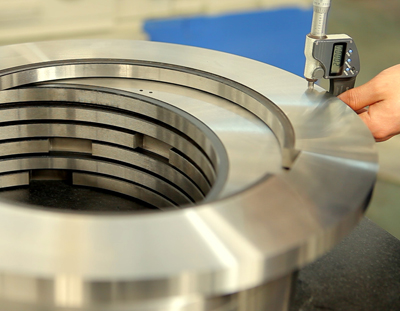
Figure 1 Precision Pre-inspection of Slitting Knife