Ultra-high-precision Shim-free Metal Coil Slitting — GOODKLIFE
Views : 2847
Author : Mr. Jiang
Update time : 2023-04-11 21:04:00
With the rapid development of economy, all walks of life have put forward higher and higher requirements for the precision slitting of sheet metal. These requirements are nothing more than two aspects of improving slitting quality and reducing slitting costs, such as smaller burrs, higher strip width accuracy, longer tool life, and more convenient knife assembly. Precision slitting of thin metal sheets is a systematic project involving many factors. This article focuses on the importance of slitting circular knives in precision slitting.
1 The accuracy of the circular slitting knife
1.1 Flatness and Parallelism
Sufficiently high flatness and parallelism are necessary conditions to ensure that the shear clearance between the upper and lower slitter blades of the slitting machine is always consistent during dynamic operation. Correct clearance is at the heart of ensuring precision cutting. If the surfaces of circular knives are not flat, or the two sides of the blade are not parallel, the gap between the upper and lower blades is always changing. In addition, In addition, the reaction force generated by the extrusion of the strip during slitting also causes the gap to change continuously. This will make it impossible to get burr-free strips. For example, to cut a stainless steel sheet with a thickness of 0.07 mm, the gap requirement is 7 μm, but if the flatness and parallelism of the blade face are within 5 μm (this is quite high precision in the machining industry), then the gap error will be as high as 50%. As for the problems that burrs will bring to the processing and quality of downstream products, this article will not repeat them.
1.2 Knife thickness tolerance
The thickness tolerance of the blade is mainly to ensure the cutting accuracy of the width of the metal strip and prevent the cumulative error in the knife assembly. If a blade with a thickness tolerance of 1~2 μm or even 0.5 μm cannot be provided, the cumulative error when multiple shearing knives are assembled is unavoidable. Refer to Table 1 for the thickness tolerance that the blade should have when precision slitting.
1 The accuracy of the circular slitting knife
1.1 Flatness and Parallelism
Sufficiently high flatness and parallelism are necessary conditions to ensure that the shear clearance between the upper and lower slitter blades of the slitting machine is always consistent during dynamic operation. Correct clearance is at the heart of ensuring precision cutting. If the surfaces of circular knives are not flat, or the two sides of the blade are not parallel, the gap between the upper and lower blades is always changing. In addition, In addition, the reaction force generated by the extrusion of the strip during slitting also causes the gap to change continuously. This will make it impossible to get burr-free strips. For example, to cut a stainless steel sheet with a thickness of 0.07 mm, the gap requirement is 7 μm, but if the flatness and parallelism of the blade face are within 5 μm (this is quite high precision in the machining industry), then the gap error will be as high as 50%. As for the problems that burrs will bring to the processing and quality of downstream products, this article will not repeat them.
1.2 Knife thickness tolerance
The thickness tolerance of the blade is mainly to ensure the cutting accuracy of the width of the metal strip and prevent the cumulative error in the knife assembly. If a blade with a thickness tolerance of 1~2 μm or even 0.5 μm cannot be provided, the cumulative error when multiple shearing knives are assembled is unavoidable. Refer to Table 1 for the thickness tolerance that the blade should have when precision slitting.
Table 1 Goodklife Circular Knife Tolerance
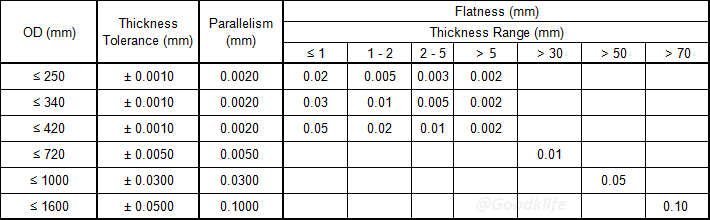
1.3 Surface roughness
A good surface roughness of the blade surface can improve the rigidity of the entire shearing system, increase the sharpness of the blade, reduce micro cracks on the blade and prolong the life of the blade. Different machining processes can result in different surface finishes (Figure 1). For high-precision non-ferrous metal processing, it is generally necessary to choose 0.05 - 0.1 μm. For slitting other thin coils, a surface roughness of 0.1 - 0.2 μm can be chosen.
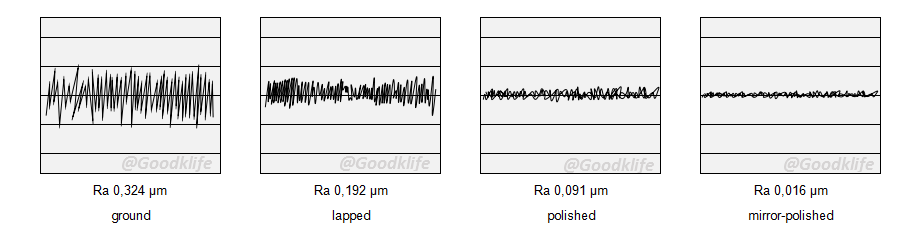
Figure 1 Surface Quality of Slitter Blades with Different Processing
1.4 Inner circle tolerance
The inner circle tolerance of the blade and rubber ring should be controlled within H6 and H7 to reduce their radial runout. In order to adapt to the cutting of thin materials (such as 0.05 mm material), the radial runout will be more strictly controlled, and they must use expansion shafts. At this time, the inner circle tolerance should be controlled within 0.01 mm.
Accuracy Guaranteed: All tool accuracy is guaranteed to be correct. In case of discrepancies, customers can choose un-conditional refund or re-production for free. However this will never happen. |
2 Selection of knife material
Different customers cut different materials. Even for the same customer, different materials are often cut on the same slitting machine. In this way, there are different requirements for the wear resistance and sharpness of the blade. And the material itself is not omnipotent. Often, materials with good wear resistance and sharpness have poor impact resistance, and materials with good impact resistance have poor wear resistance and sharpness. Therefore, different blade materials should be chosen for different cutting materials.
Table 2 is the recommended steel material for slitting disc knives from Goodklife.
Table 2 Material Selection for Slitter Knife from Goodklife
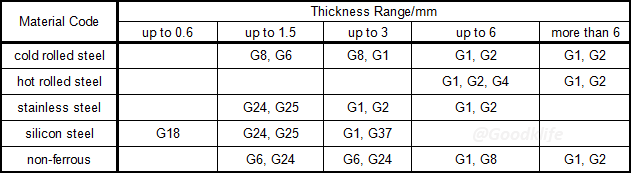
Generally speaking, when cutting thick plates, the blade should choose materials with good impact toughness, and the blades for cutting thin plates should choose materials with good wear resistance and sharpness. Mixed shearing of different materials is the most difficult to manage, but for small companies where mixed shearing is necessary, a blade with a compromise in material properties is recommended.
3 Correct use of tools and spacers
After you have a good machine and blade, you should also use the knife and assembling knife correctly.
3.1 Slitter Tool Accuracy Reclassification
The re-grouping of precision blades can greatly improve the precision of blade assembling and eliminate accumulated errors. Since it is impossible for a manufacturer to produce blades of absolutely the same thickness, there is always some allowable error. And the slitting machine is composed of many basic cutting units, and each unit is composed of many knives, bonded stripper rings and spacers. Even the most precise blades that fully meet the requirements of the drawings will have accumulated errors after tens or hundreds of blades are stacked together. In order to completely eliminate the accumulated error, the user must group the blades so as to improve the accuracy of the blade assembly. A knife with poor precision cannot use software because no one knows its actual size value. The grouping is to divide all blades and rubber bonded stripper rings, spacers with a tolerance within +/- 1 μm into three groups according to their thickness tolerances -1 μm to -0.3 μm, -0.3 μm to 0.3 μm, 0.3 μm to 1 μm, respectively Marked with "-", "0", "+" marks. When assembling tools, use the principle of "+" and "-" to offset, and put tools (slitter knives, bonded stripper rings and spacers) with zero total error together as much as possible, thereby reducing the gap error of each unit and the total accumulated error. Figure 2 shows the slitting tools marked with "+", "0" and "-" produced by Goodklife Machinery Technology.
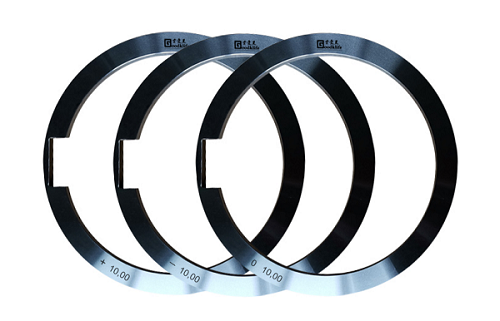
Figure 2 Slitting Tools Marked With "+", "0" and "-" Produced by Goodklife
3.2 Software GSAP support (Goodklife Slitting Assembling Program)
The computer software GSAP specially designed by Goodklife can consciously select "0", "+", "-" tools, and tell the operators the quantity they need, and the operators can directly assemble slitting tools according to the software outputs. The efficiency and precision of slitting tools assembling can be greatly improved. With the help of this software, the clearance accuracy of the knives can be greatly improved, the inventory of the knives can be reduced, the time of slitting tools assembling can be shortened, and the utilization rate of coils can be improved, which is very beneficial to the management of production and tools.
3.3 Selection of knife clearance
The clearance of the blade has a very close relationship with the thickness and strength of the material to be sheared (Figure 3). Moreover, in the process of shearing, the material to be sheared is not 100% sheared, but part of the thickness is sheared and part is pulled off.
The computer software GSAP specially designed by Goodklife can consciously select "0", "+", "-" tools, and tell the operators the quantity they need, and the operators can directly assemble slitting tools according to the software outputs. The efficiency and precision of slitting tools assembling can be greatly improved. With the help of this software, the clearance accuracy of the knives can be greatly improved, the inventory of the knives can be reduced, the time of slitting tools assembling can be shortened, and the utilization rate of coils can be improved, which is very beneficial to the management of production and tools.
3.3 Selection of knife clearance
The clearance of the blade has a very close relationship with the thickness and strength of the material to be sheared (Figure 3). Moreover, in the process of shearing, the material to be sheared is not 100% sheared, but part of the thickness is sheared and part is pulled off.
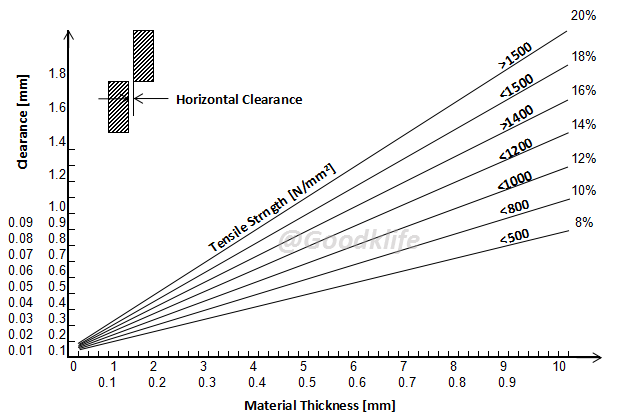
Figure 3 Slitter Knife Clearance Chart
3.4 Determination of the overlapping of the upper and lower blades
It can be seen from Figure 4 that the overlap is the largest when the thickness of the processed material is 1.2 mm. When the thickness is below 1.2 mm, the overlap increases with the thickness; when it exceeds 1.2 mm, the overlap decreases with the thickness.
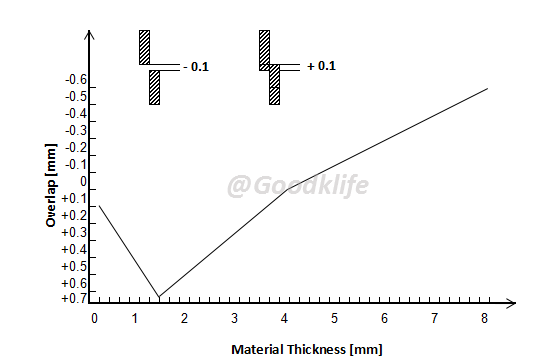
Figure 4 Slitter Knife Overlap Chart
3.5 Parallelism accuracy of slitting arbors
Machine precision and blade precision are the two most fundamental elements to ensure precision cutting. After the machine has been running for a period of time, each sheet metal processing enterprise is required to keep abreast of whether its accuracy has changed. Figure 5 shows the parallelism accuracy requirements of the upper and lower arbors of the slitting machine.

Figure 5 Accuracy Requirements of the Upper and Lower Arbors of the Slitting Machine
For more information, you are welcome to contact us anytime. We are also actively looking for broader cooperation. As long as you are a steel mill with a certain scale, a well-known local metal processing or manufacturer, you will have the opportunity to use our sample products for free.